Think Big
August 2, 2023
Every Thursday at 3:15 pm, Hatteras Improves
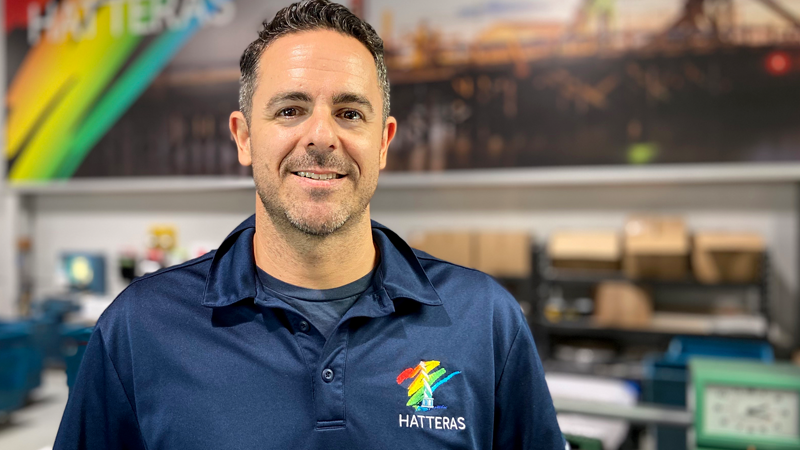
# Commercial Print
# Digital Printing
# Operations
The company’s weekly operations meeting spotlights its pursuit of perfection and culture of teamwork
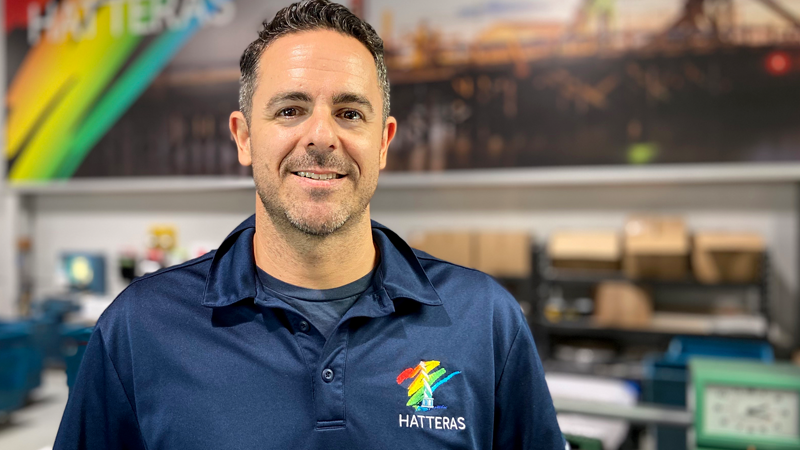
It’s 3:15 p.m. Eastern on Thursday, which means Ryan Devesty’s notes are ready.
As the hum of presses fills the air, Hatteras team members from multiple shifts gather for the weekly “Hatteras Huddle” — an operations-focused meeting where they review fundamentals, discuss current goals, address challenges and celebrate successes.
Each week, the half-hour gathering in Hatteras’ Tinton Falls, NJ, headquarters buzzes with camaraderie and a sense of purpose. It’s a mix of fine-tuning and fist-bumps that has helped Hatteras drive eye-opening results for top brands.
Four years ago, Hatteras had a hiccup in its HP Indigo room — a digital front end (DFE) issue that caused a delay in getting some files to press — and Devesty solved it quickly. He was promoted on the spot, and now serves as the company’s Director of Digital Print and Workflow Solutions. In the role, he’s equal parts friendly and focused — a heart and mind that has helped to boost the company’s stellar reputation for speed and service.
The team is ready for the meeting, which begins the same way each time — a quick review of fundamentals such as safety and data-collection procedures. The entire Hatteras team embraces the goal of accurate workflow data, which helps leaders make key decisions and also helps the estimating team work with precise, updated information.
Meeting participants also review operator tasks that might seem mundane, but absolutely matter to an ISO-certified company that’s never satisfied with the status quo — cleaning rollers, wiping wiper blades, checking consumables and so on.
Devesty handles these huddles as a persistent yet supportive coach might handle a team of talented athletes: Everyone tagging jobs before they move to the next process? How many blemishes or hickeys on printed flat sheets did we spot since last week? Any non-compliant events to address? Also, what are the most exciting opportunities we have to improve? Which operators here went above and beyond for a client job and deserve recognition? Who wants to chat about whatever is on their mind?
“The meeting is a reminder that we are all in this together,” Devesty says. “It’s working, because we’re seeing a decline in non-compliance issues, trying to catch them all beforehand. We now take notes from similar jobs and can produce the next one slightly differently if we need to, starting in the production-planning stage, well before it even gets to the manufacturing floor.”
Efficient workflow is Hatteras’ heartbeat
As a family-owned business, Hatteras has come a long way since its modest beginnings in the 1980s. Starting in a small airplane hangar, it quickly expanded and advanced. Today, it’s a $65 million company with three buildings — one housing large-format printing, fulfillment and assembly, and the other handling digital printing, offset printing, binding and mailing. The company also invested in nearby warehouse space to increase its capacity for raw materials and finished goods storage.
Its diverse range of applications is eye-opening, and over the past three years, Hatteras’ HP Indigo volume has doubled from 60 million impressions to 120 million.
"Our journey has been one of growth, fueled by our commitment to invest in people and embrace cutting-edge technology,” Devesty says.
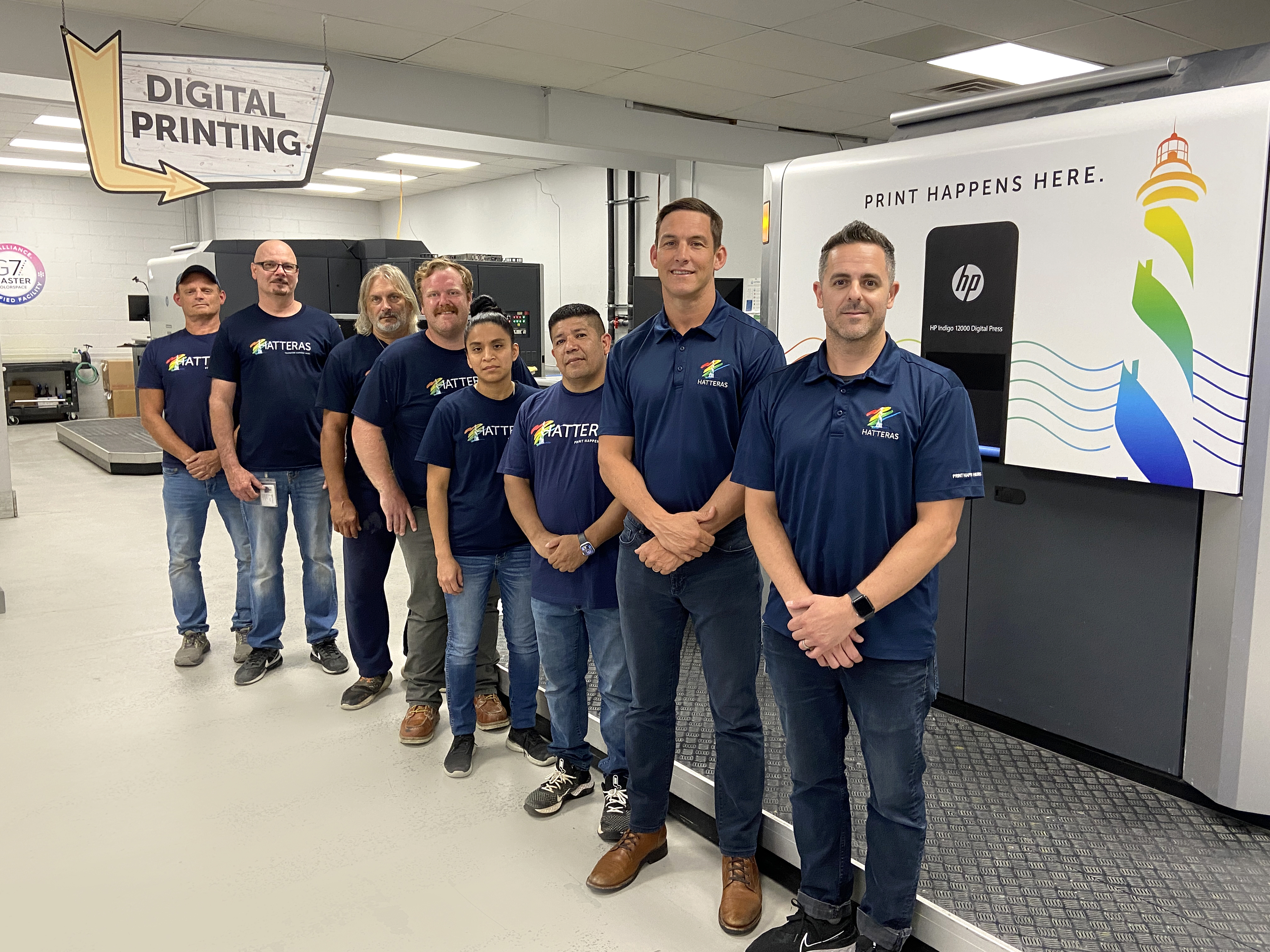
Automated workflows combined with variable data technology have been a big driver of success with Hatteras’ digital platform. Some programs are essentially on autopilot (thanks to the program onboarding expertise of Hatteras’ Integrated Solutions team), whereby data files arrive at 5 a.m. each day, and as many as several hundred thousand personalized pieces are dropped in the mail the same day.
Hatteras relies on HP’s PrintOS system to maximize productivity, improve quality and increase automation in the manufacturing process. The PrintOS application Color Beat gives the team real-time color status and reports so they can maintain color accuracy and consistency across all jobs and presses. Essentially, it replaces 20- to 30-minute manual processes with an automated solution that takes about one minute and gives operators immediate insight into color calibration. “If you read into the data and read the story it’s leaving you, you can realize the root cause of an issue and quickly change a bid base, a roller, a blanket, and do some quick adjustments,” Devesty says.
Maintaining workflow efficiency has been especially important to Hatteras as the company has grown. Adding new machines and new managers causes technical and HR headaches for many printers, but not at Hatteras, where department managers are responsible for drafting and tweaking procedures that are approved or adjusted by upper management and the compliance team. All department employees are continually trained on those procedures and can reference them quickly when needed.
Hatteras especially needed that high level of organization when it ventured into packaging several years ago. The company quickly discovered just how much the capability demands meticulous precision.
Today, for many packaging projects handled by Hatteras, each piece is both an exact science and a work of art. For example, the multinational conglomerate Sony Corporation is a key client, and musicians represented by Sony occasionally visit Hatteras to see samples of vinyl album covers and other printed pieces. When you’re completing a sequel project for Bruce Springsteen, which the company recently did, there’s no room for scuffing on a folder/gluer in the bindery or a slight skew that makes the box fold incorrectly. The real Boss is quality control.
Today, for many packaging projects handled by Hatteras, each piece is both an exact science and a work of art. “Every box we produce is destined for retail, and we treat each one as a masterpiece,” Devesty says. “From a robust quality assurance team to thorough checks at every stage of production, we strive for perfection with each piece that leaves our facility.”
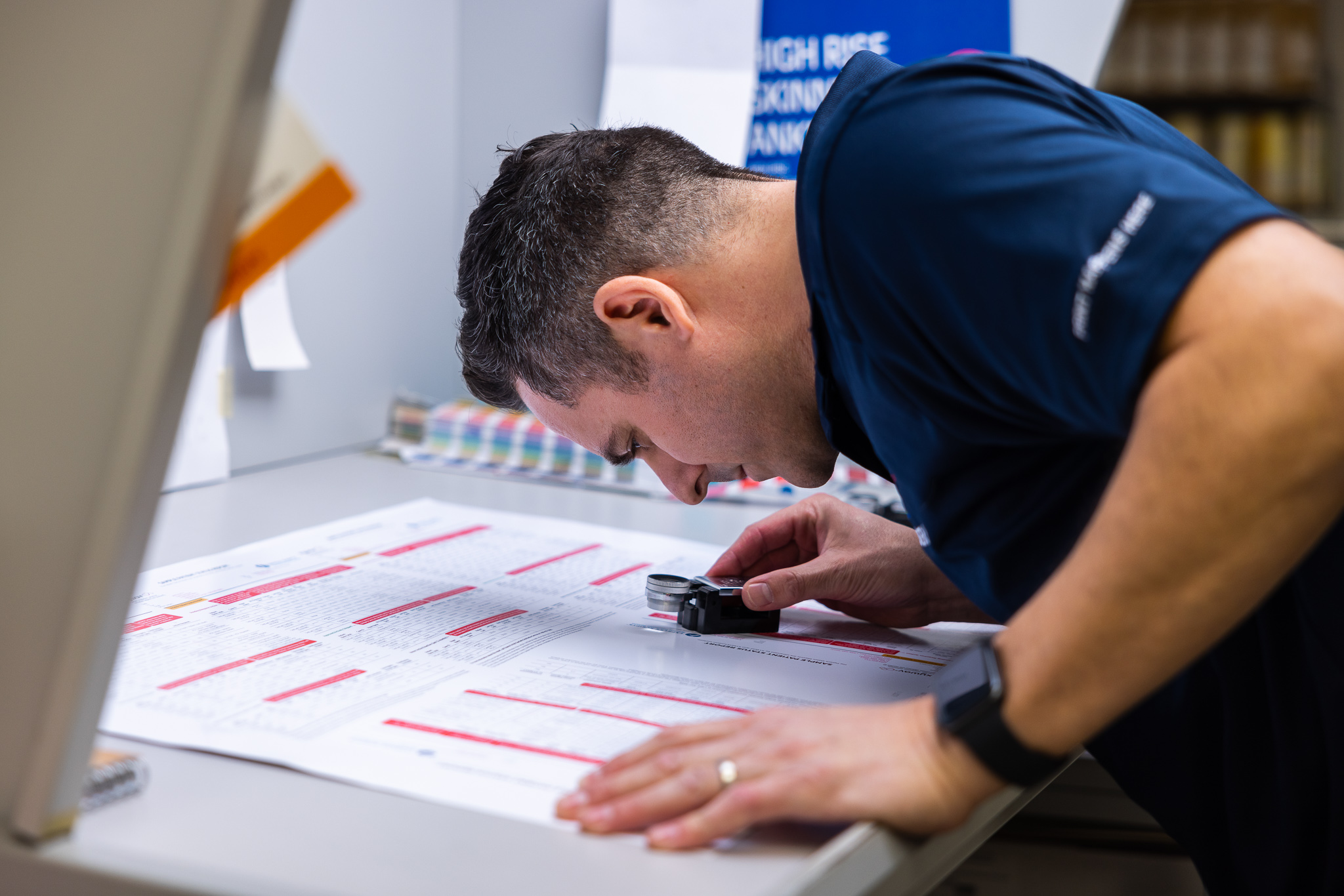
A place where talent and teamwork combine
Charts, graphs, data, reports, metrics and key performance indicators keep the Hatteras team accountable and on track, but the combined efforts and commitment of team members propel the firm forward.
In 2023, Hatteras was named one of New Jersey’s Top Workplaces by NJ.com, placing the company among an exclusive list of only 25 mid-sized companies (between 150-499 employees) to have achieved the honor. Companies were measured against 15 culture drivers that are important to organizational success, including alignment, execution and connection.
“I’m incredibly proud of our team, and humbled by their view of the company that has led us to be ranked among the top workplaces in the state,” said Hatteras President Bill Duerr. “In the print industry, which is highly service-driven, our employees are our most valuable asset, so ensuring that we provide a rewarding environment that allows our staff to grow both professionally and personally is of utmost importance.”
That’s especially true when you’re growing. When finding talent for new positions — a major issue for Dscoopers across the globe — Hatteras often finds the right fit in a current employee thanks to cross-department training and ongoing skill development. By recognizing the potential in existing employees and providing them with opportunities to grow, "we’re cultivating a workforce that is agile and well-versed in the art of printing,” Devesty says.
He points to something Earvin “Magic” Johnson said during his keynote at the 2023 Edge St. Louis World Expo: “You want to be ready, instead of getting ready.” For Hatteras’ quality-assurance team and other personnel, that means staying ahead of the curve through communication and preparation, not frantically trying to play catch-up on projects. “We’re able to keep our presses ready for any volume at any moment,” Devesty says.
He's quick to credit Duerr and the entire Hatteras team for embodying a customer-first mindset. “We're always looking to over-deliver; that's a big part of our culture,” Devesty says. “We understand the importance of spending just a little more time on those color-critical jobs. We're also now bringing a lot of customers into the shop, where our president is right there on the shop floor to greet them and make sure they’re getting what they need.”
What’s next for this remarkable team? How can they advance even further?
Check back Thursday at 3:15 p.m.
“Together,” Devesty says, “we’re fine-tuning the art of printing.”
Sign in or Join the community
Innovating Print, Together
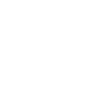
Create an account
Innovating Print, Together
Dive in
Related
3:22
video
Security in Every Pixel: How Jura is Powering the Next Era of Print Protection
Jun 5th, 2025 • Views 20
3:22
video
Security in Every Pixel: How Jura is Powering the Next Era of Print Protection
Jun 5th, 2025 • Views 20